In recent years, composite materials have been used more and more in various fields of science and technology due to their unique properties, especially in aircraft, automotive, defense and aerospace, as well as other advanced industries. However, due to the heterogeneity of composite materials and the wear resistance of reinforcing materials, the machining of composite materials has become a very complicated work. Today we will discuss the types, properties and machining techniques of composite materials.
1. Types and properties of composite materials
A. Types of composite materials
Composite material is a new material that people use advanced material preparation technology to optimize the combination of material components with different properties. Composite materials are generally defined to meet the following conditions:
a. Composite materials must be man-made, materials that people design and manufacture according to their needs;
b. The composite material must be composed of two or more material components with different chemical and physical properties in the designed form, proportion and distribution, and there is a clear interface between the components;
c. It has structural designability and can be designed for composite structures;
d. The composite material not only maintains the advantages of the properties of each component material, but also obtains comprehensive properties that cannot be achieved by a single component material through the complementarity and correlation of the properties of each component.
The matrix materials of composite materials are divided into two categories: metal and non-metal. Commonly used metal substrates are aluminum, magnesium, copper, titanium and their alloys. Non-metallic substrates mainly include synthetic resin, rubber, ceramics, graphite, carbon, etc. Reinforcing materials mainly include glass fiber, carbon fiber, boron fiber, aramid fiber, silicon carbide fiber, asbestos fiber, whisker, and metal.
B. Properties of composite materials
Among all composite materials, fiber-reinforced materials are widely used. Fiber-reinforced materials are characterized by large specific modulus, small specific strength and specific gravity.
This paper mainly analyzes the machining technology of carbon fiber reinforced materials. The cutting characteristics of carbon fiber composite materials are: the tool wear is relatively serious, residual stress will be generated, the material will be delaminated and the cutting temperature will be high. Delamination failure refers to the debonding phenomenon between the composite plies, and the debonding phenomenon is closely related to the cutting parameters. If the parameters are unreasonable, it will easily lead to the occurrence of degumming, and even greatly affect the material properties, resulting in the scrap of parts.
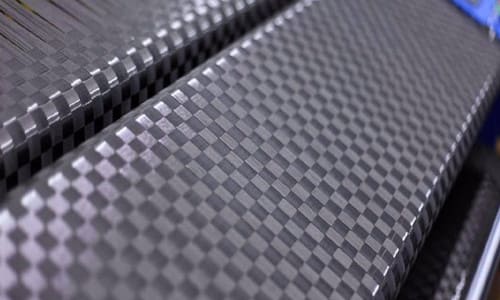
During the cutting process, the cutting temperature should not be too high, otherwise the difference between the expansion coefficients of the reinforced composite material and the matrix resin will be too large, resulting in residual stress. In addition, the narrow area around the cutting edge of the tool is where the cutting temperature is higher, and the thermal conductivity of the carbon fiber composite material is poor, so this heat transfer to the workpiece and the tool can damage the carbon fiber composite material.
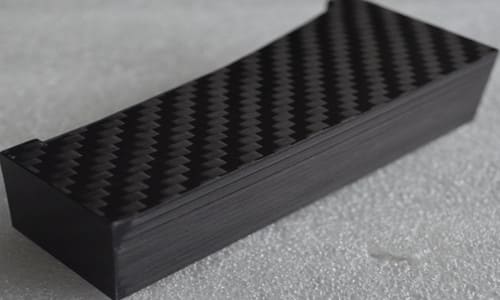
2. Analysis of composite materials machining technology
A. Metal matrix composite materials machining
Metal matrix composite material refers to a material in which the matrix is an alloy or pure metal, and the reinforcement is generally a composite of particles, fibers and crystals. This type of composite material is characterized by high shear and constant strength, and good comprehensive properties such as fatigue resistance and toughness. In addition, it also has the characteristics of no pollution, small coefficient of thermal expansion, no aging, electrical conductivity, thermal conductivity, no moisture absorption and wear resistance.
In some traditional processes, metal-based composite materials are usually used in machining, such as grinding, cutting, milling and turning. However, the use of such traditional processes will lead to mechanical wear. Therefore, it is necessary to select tools containing diamonds, diamond-tipped tools, high-speed steel, and tungsten carbide, and relevant personnel must master the cutting speed and add lubricants or coolants. Only in this way can achieve better machining results.
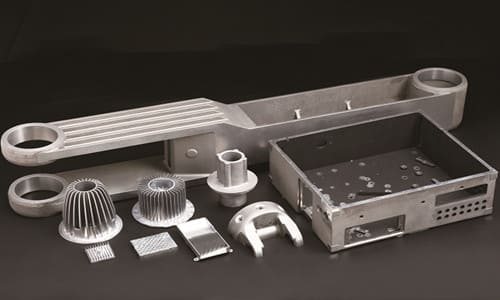
B. Thermoplastic resinmatrix composite materials machining
The thermoplastic resin matrix composite material generally refers to a composite material with thermoplastic resin as the matrix. When machining this material, if the temperature is too high, it is easy to scorch or soften the matrix of the material. In order to avoid overheating during machining, appropriate coolant should be added. During the cutting process, it is necessary to ensure that the chip flute of the cutting tool has sufficient capacity and maintain a fast cutting speed. The turning tool and the tool head should be sharp, as far as possible, use emery or tungsten carbide tools, and some special plastics can use high-speed steel tools. The lane should be ground at an inclination to reduce the cutting force of the tool and facilitate cutting.
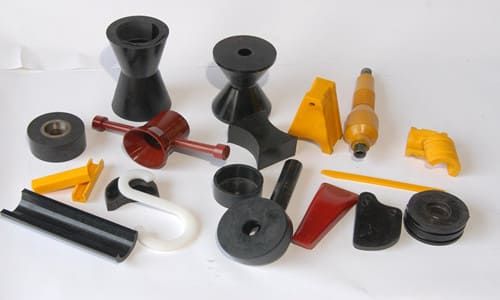
C. FRPmachining
The characteristics of FRP include corrosion resistance, high hardness, brittleness, high temperature resistance, and good transparency. According to the resin composition, it can be divided into unsaturated polyester resin matrix, epoxy resin matrix and phenolic resin matrix. The machinability of FRP is closely related to the resin base. Usually, the difference in resin matrix will affect the machinability of FRP. It is found from previous experiments that the wear of FRP tools in high-speed cutting is very serious. Therefore, when cutting, cubic boron nitride tools or diamond tools can be replaced, and using these tools to cut FRP can greatly improve production efficiency. When selecting the geometric parameters of the tool, it is necessary to master the scientific laws and select the properties of the installation materials.
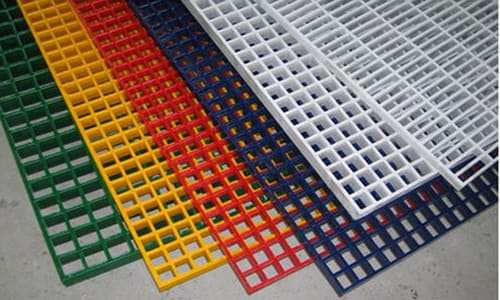
3. Composite materials machining methods
Typically, the machining process of composite materials is: sawing-grinding-milling-turning-cutting-copying-drilling. And composite materials have more advanced machining methods, such as electrochemical machining, laser beam machining, electron beam machining, high pressure water cutting, electrical discharge machining and ultrasonic machining.
When machining composite materials, relevant personnel should attach great importance to the stability of composite material cutting, select cutting temperature scientifically and reasonably, and conduct in-depth analysis to study the cutting method of new cutting tools, so as to improve the quality of composite material machining. In addition, we can also use electron microscope to observe the pore walls of carbon fiber composite materials to explore the optimization method of composite machining and ensure the smooth progress of carbon fiber composite material machining.