As industries like medical, aerospace, electronics, and precision instruments continue to demand smaller, more complex components, CNC machining of small or intricate parts has become more critical than ever. However, machining miniature parts comes with a unique set of challenges that require specialized tools, strategies, and expertise.
In this blog, we explore the key challenges of CNC machining small or intricate parts, and how manufacturers can overcome them to achieve exceptional precision and reliability.
1. Maintaining Tight Tolerances
One of the biggest hurdles in machining small parts is maintaining tight tolerances. Even the slightest deviation in dimensions can render a micro component unusable, especially in medical or aerospace applications.
✅ Solution:
-
Use high-precision CNC machines with sub-micron accuracy.
-
Implement real-time quality control systems such as laser measurement or coordinate measuring machines (CMM).
-
Control environmental conditions (e.g., temperature) to reduce expansion or contraction that can affect tolerance.
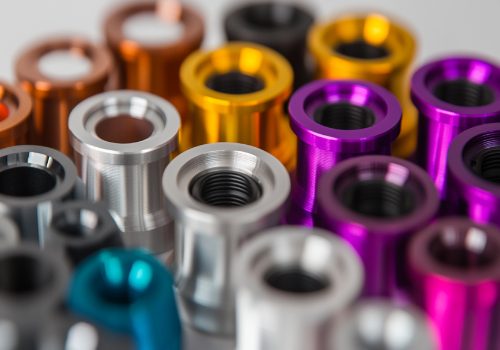
2. Tooling Limitations
Standard cutting tools are often too large or imprecise for delicate features like micro-holes, thin walls, or sharp corners.
✅ Solution:
-
Use micro-tools designed specifically for intricate work.
-
Opt for high-rigidity, low-runout spindles to prevent vibration and tool deflection.
-
Choose tools with ultra-fine grain carbide or diamond coatings for enhanced precision and wear resistance.
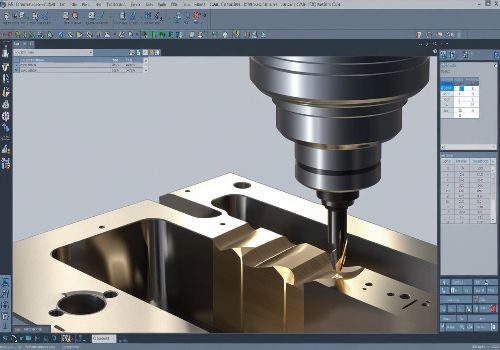
3. Workholding and Fixturing
Clamping or securing small parts without damaging or distorting them is a critical challenge. Even slight movement during machining can lead to errors or scrapped parts.
✅ Solution:
-
Use custom micro-fixtures, vacuum chucks, or magnetic bases for secure holding.
-
Apply soft jaws or polymer inserts to avoid surface marring.
-
Design multi-part fixturing systems to increase throughput while minimizing handling.
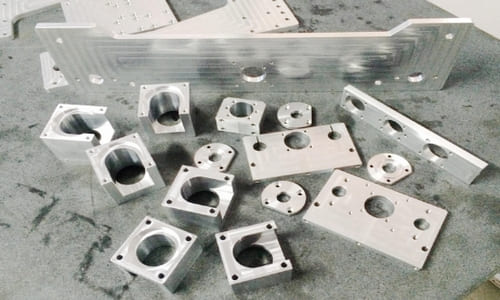
4. Heat Generation and Tool Wear
Due to the small surface area, heat from cutting can quickly build up, causing tool wear, workpiece deformation, or poor surface finish.
✅ Solution:
-
Utilize coolant-through tools or apply minimum quantity lubrication (MQL).
-
Use high-speed spindles with optimized cutting parameters to balance heat and chip removal.
-
Monitor tool wear in real-time and replace tools proactively.
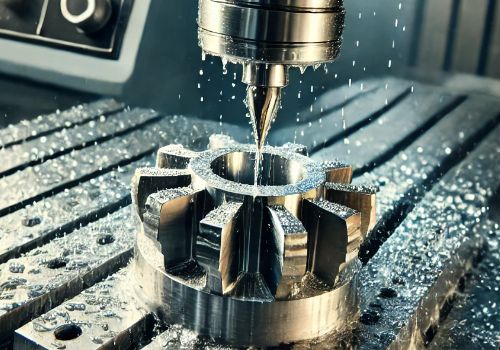
5. Chip Removal
In micro-machining, chip evacuation is often more difficult. Chips can clog the cutting zone, scratch the surface, or cause tool breakage.
✅ Solution:
-
Use high-pressure coolant or air blasts to remove chips efficiently.
-
Design tool paths with chip clearance in mind.
-
Avoid deep cuts that generate excess material buildup.
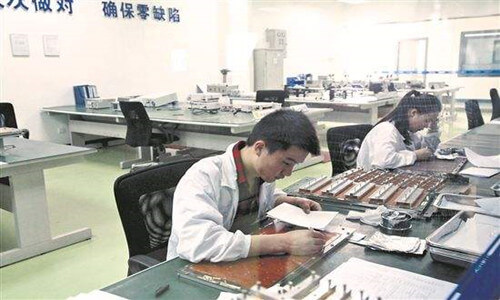
6. Programming Complexity
Machining intricate geometries often involves complex 3D surfaces, sharp transitions, or tight internal radii that are hard to program with standard CAM operations.
✅ Solution:
-
Leverage advanced 5-axis CNC machining for better tool access.
-
Use high-resolution CAD models and specialized CAM software capable of high-density toolpath generation.
-
Simulate toolpaths virtually before production to catch potential collisions or inefficiencies.
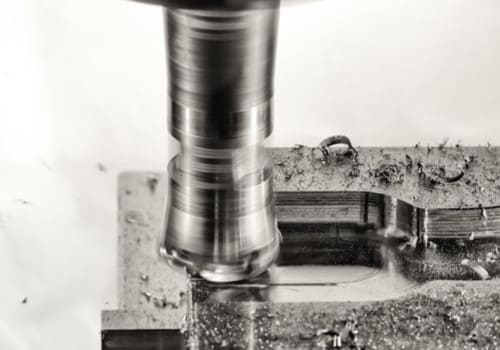
7. Inspection and Quality Control
Inspecting micro components is often more difficult than machining them. Traditional gauges or manual tools may not be effective or precise enough.
✅ Solution:
-
Use non-contact inspection systems such as laser scanners or vision systems.
-
Implement automated part inspection right on the CNC machine (in-process metrology).
-
Record data for traceability and compliance in regulated industries.
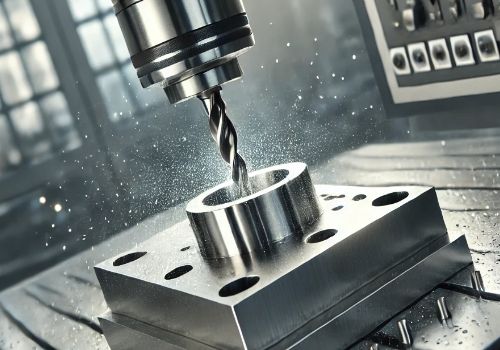
Partnering with the Right CNC Machining Supplier
Successfully machining small or intricate parts is not just about having the right equipment—it’s about experience, engineering know-how, and attention to detail. At DO machining, we specialize in high-precision CNC machining of miniature and complex components for demanding industries.
Our team combines state-of-the-art machinery, tight process control, and custom solutions to deliver parts that meet your exact requirements—on time and on budget.
Conclusion
While CNC machining small or intricate parts comes with many challenges, they can be effectively addressed through advanced tooling, precise programming, proper workholding, and expert handling. Whether you need micro-machined components for medical devices, aerospace assemblies, or high-end electronics, choosing a capable machining partner is essential to ensure performance and reliability.
👉 Ready to get started? Visit https://www.domachining.com to learn more about how we can help you bring your most detailed designs to life.