Introduction
Repeatability is the backbone of precision CNC machining. Whether you’re producing high-volume parts or complex prototypes, a well-designed CNC fixture ensures consistent accuracy across multiple production runs. Poor fixture design leads to misalignment, part movement, and scrapped components—costing time and money.
In this guide, we’ll explore how to design CNC fixtures for maximum repeatability, covering materials, clamping strategies, and best practices to optimize your machining process.
What Makes a CNC Fixture Repeatable?
A repeatable CNC fixture must:
✔ Securely hold the workpiece without deformation
✔ Maintain precise alignment across multiple setups
✔ Allow quick loading/unloading for efficiency
✔ Minimize vibration and deflection during machining
Key Steps to Designing Repeatable CNC Fixtures
1. Define Part Requirements
-
Tolerances: How precise must the fixture be? (±0.001″ or tighter?)
-
Material: Will the fixture handle aluminum, steel, or composites?
-
Production volume: High-volume needs quick-change features.
2. Choose the Right Fixture Material
Material | Best For | Pros | Cons |
---|---|---|---|
Tool Steel (D2, A2) | High-wear applications | Durable, long lifespan | Expensive |
Aluminum (6061-T6) | Light/medium-duty | Lightweight, easy to machine | Less rigid than steel |
Plastic (Delrin, UHMW) | Non-marring applications | Prototyping, soft materials | Wears faster |
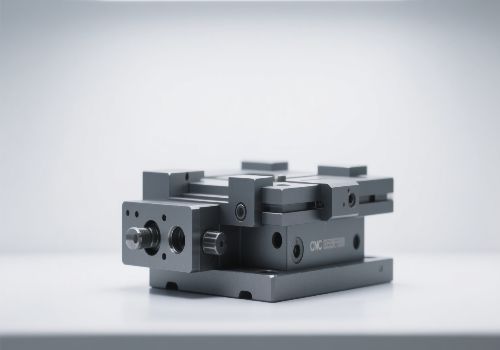
3. Optimize Clamping Strategy
-
Use Locating Pins – Ensure part alignment is consistent.
-
Apply Even Pressure – Avoid distortion with balanced clamps.
-
Minimize Overhang – Reduces vibration and deflection.
4. Incorporate Modular Design
-
Quick-change jaws for different part sizes.
-
Standardized mounting (e.g., Mitee-Bite clamps, dowel pins).
5. Minimize Setup Errors
-
Use Datum Features – Align parts to a fixed reference.
-
Add Foolproofing (Poka-Yoke) – Prevent incorrect loading.
6. Test & Validate Fixture Repeatability
-
Run test batches to check consistency.
-
Measure part dimensions after multiple cycles.
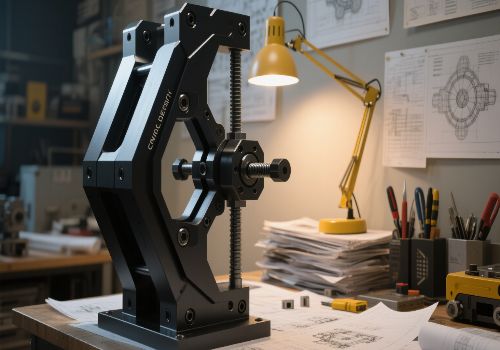
Best CNC Fixture Types for Repeatability
-
Vise Fixtures – For prismatic parts with soft jaws.
-
Plate Fixtures – Custom-machined plates with locating pins.
-
Tombstone Fixtures – Multi-sided machining in vertical mills.
-
Hydraulic/Pneumatic Fixtures – Automated clamping for high volume.
-
Magnetic Fixtures – For ferrous metals in grinding/EDM.
Common Fixturing Mistakes to Avoid
❌ Poor support for thin-walled parts (causes deflection)
❌ Overcomplicating the design (increases setup time)
❌ Ignoring thermal expansion (alters tolerances over time)
❌ Using worn-out components (reduces accuracy)
Advanced Tips for High-Precision Fixtures
✔ Use Kinematic Coupling – Ultra-precise repeat positioning.
✔ Add Quick-Release Clamps – Faster changeovers.
✔ Implement RFID Tagging – Track fixture wear and usage.
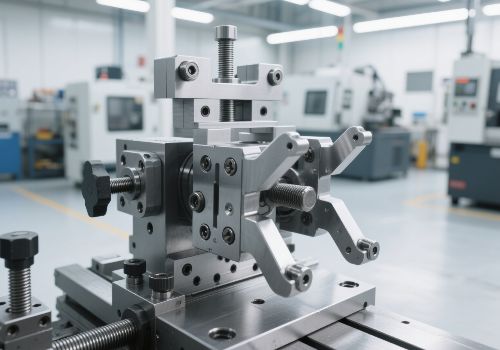
Conclusion
Designing a repeatable CNC fixture requires strategic planning, robust materials, and smart clamping solutions. By focusing on precision alignment, modularity, and validation, you can ensure consistent part quality and reduce scrap rates.
Need custom CNC fixtures for your shop? Get a quote today for high-repeatability workholding solutions!