Introduction
As sustainability becomes a priority in manufacturing, green machining offers a way to reduce environmental impact while maintaining efficiency. By optimizing toolpaths, materials, and energy use, manufacturers can cut waste, lower costs, and meet eco-friendly goals.
In this guide, we’ll explore the top green machining practices, their benefits, and how to implement them in your CNC operations.
What Is Green Machining?
Green machining refers to eco-conscious manufacturing techniques that minimize waste, energy consumption, and hazardous materials. Key goals include:
✔ Reducing material waste
✔ Lowering energy usage
✔ Eliminating toxic coolants
✔ Improving recycling efforts
Top 10 Green Machining Practices
1. Optimize Toolpaths for Efficiency
-
Use High-Speed Machining (HSM) to reduce cycle times
-
Implement adaptive toolpaths to minimize air cutting
-
Choose trochoidal milling for lower energy consumption
2. Switch to Dry Machining (When Possible)
-
Eliminates coolant waste
-
Best for aluminum, cast iron, and some steels
-
Requires specialized tool coatings (e.g., TiAlN)
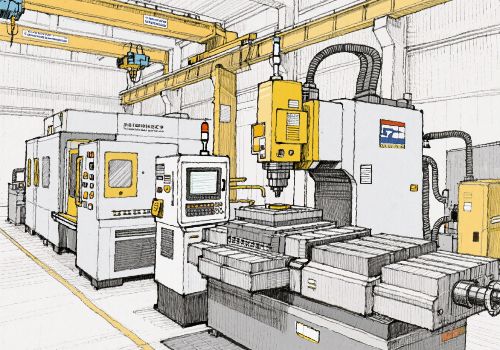
3. Use Minimum Quantity Lubrication (MQL)
-
Applies a fine mist of coolant instead of flood cooling
-
Reduces fluid waste by up to 90%
-
Extends tool life
4. Recycle Metal Chips & Coolants
-
Chip compactors reduce scrap volume
-
Coolant recycling systems filter and reuse fluids
-
Sell scrap metal to recyclers
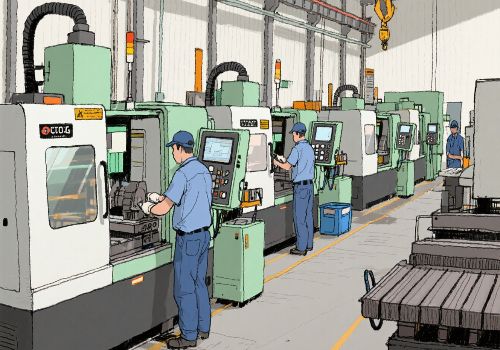
5. Choose Sustainable Materials
-
Recycled metals (e.g., aluminum, steel)
-
Biodegradable composites
-
Avoid toxic materials like beryllium or leaded brass
6. Upgrade to Energy-Efficient Machines
-
Look for ENERGY STAR-certified CNCs
-
Use regenerative braking spindles to recover energy
-
Replace old motors with high-efficiency servos

7. Reduce Setup Waste with Digital Prototyping
-
Simulate machining before cutting to avoid errors
-
Use 3D printing for test fixtures
-
Implement CAM software with waste-reducing algorithms
8. Extend Tool Life with Proper Maintenance
-
Regularly sharpen and coat tools
-
Use tool condition monitoring to prevent premature wear
-
Store cutting tools properly to avoid damage

9. Implement Lean Manufacturing
-
Reduce idle machine time with optimized scheduling
-
Standardize processes to minimize rework
-
Adopt just-in-time (JIT) production to cut excess inventory
10. Use Eco-Friendly Workholding
-
Modular fixtures reduce material waste
-
Magnetic chucks eliminate disposable clamps
-
Reusable soft jaws instead of single-use setups
Benefits of Green Machining
✅ Lower operational costs (less waste, energy savings)
✅ Compliance with environmental regulations
✅ Improved brand reputation (eco-conscious manufacturing)
✅ Longer tool and machine life
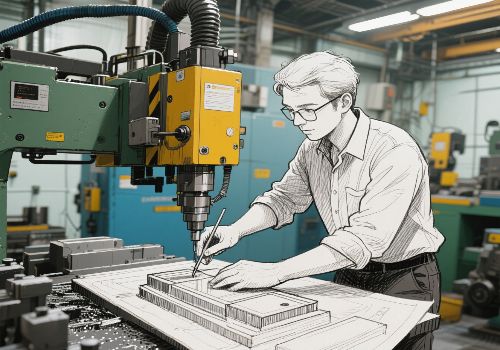
Challenges & Solutions
Challenge | Solution |
---|---|
Higher upfront costs | Long-term savings justify investment |
Limited dry machining options | Use MQL or biodegradable coolants |
Employee training needed | Implement sustainability workshops |
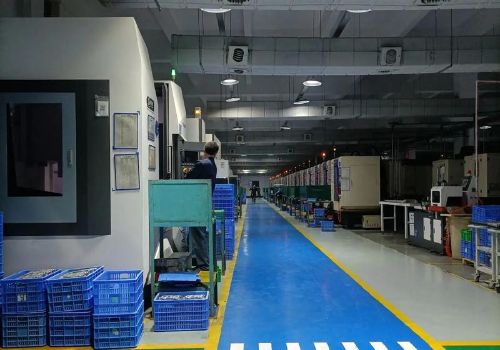
Industries Adopting Green Machining
✔ Aerospace – Lightweighting & waste reduction
✔ Automotive – Recycled materials & energy efficiency
✔ Medical – Biocompatible, non-toxic machining
✔ Consumer Electronics – Sustainable metal sourcing
Conclusion
Green machining isn’t just good for the planet—it’s good for business. By adopting energy-efficient toolpaths, dry/MQL machining, and waste-reduction strategies, manufacturers can cut costs while meeting sustainability goals.
Ready to go green? Contact us for expert advice on eco-friendly CNC solutions!