In recent years, metal crafts have become more popular. Most of the popular machines on the market will have large pieces of metal. Some high-end machines parts are made by aluminum alloy with fully CNC machining process. For aluminum parts, the most commonly used metal surface treatment process is anodizing. Today let’s take a look at the process and advantages of anodizing.
What is anodizing?
Anodizing is an electrolytic oxidation process in which the surface of aluminum alloys is usually converted into a protective, decorative and other functional oxide film.
The thickness of the anodized film is usually 5-20um, and the thickness of the hard anodized film is 60-200um. The oxide film produced by chemical oxidation generally has a thickness of 0.3-4um, which is softer, wear-resistant and corrosion-resistant than the oxide film produced by anodizing, and is rarely used alone except for special purposes.
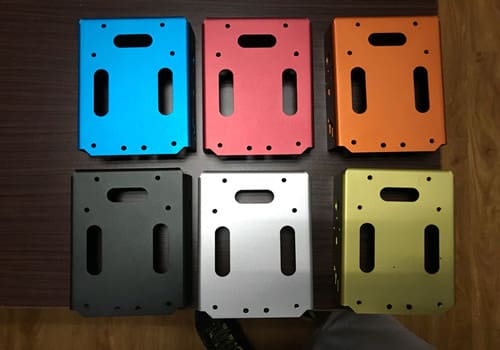
For some metal parts with high precision tolerance requirements, it is best to communicate with the anodizing factory in advance about the tolerance requirements and the film thickness before anodizing, so as to avoid the size of the metal accessories after anodizing.
Advantages of anodized surface treatment
Aluminum alloy anodizing pre-treatment technology is an important part of the work that determines the quality of the appearance design of the company’s products. The oxide film obtained by anodizing treatment also has the following characteristics:
1. Have higher hardness
The hardness of pure aluminum oxide film is higher than that of aluminum alloy aluminum oxide film, and its hardness is usually related to the alloy composition of aluminum and the process conditions of electrolyte during anodic oxidation. The anodized oxide film not only has high hardness, but also has good wear resistance, especially the porous oxide film on the surface has the ability to absorb lubricants, and can further improve the surface wear resistance.
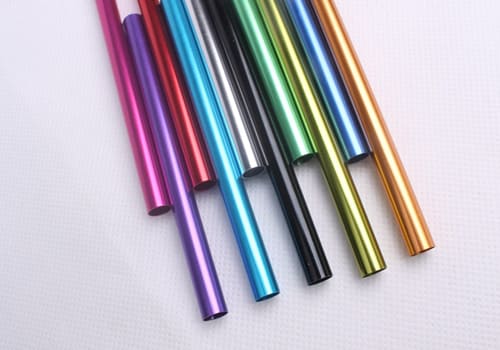
2. Have high corrosion resistance
This is due to the high chemical stability of the anodized film. Pure aluminum anodized film has better corrosion resistance than aluminum alloy anodized film, the reason is that the anodized film is discontinuous or has voids due to containing alloy components or forming metal compounds that cannot be oxidized or dissolved. Thereby greatly reducing the corrosion resistance of the oxide film. Therefore, the anodized film must be sealed to improve its corrosion resistance.
3. Have a strong adsorption capacity
Aluminum and aluminum alloy anodized film is a porous structure with strong adsorption capacity, so filling the pores with various pigments, lubricants, resins, etc. can further improve the protection, insulation, wear resistance and decorative properties of aluminum products.
4. Have good insulation properties
The anodized film of aluminum and aluminum alloy has become a good insulating material to replace the conductive properties of metal.
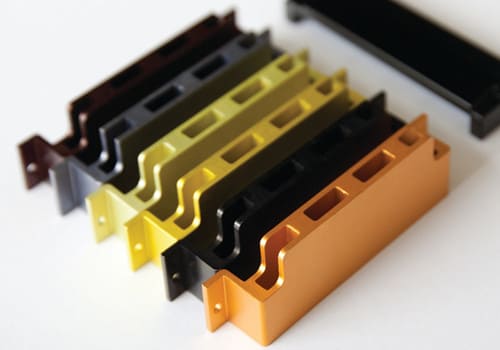
5. Have strong thermal insulation performance and heat resistance
This is because the thermal conductivity of the anodized film is much lower than that of pure aluminum, and the anodized film can withstand about 1500 °C, while pure aluminum can only withstand 660 °C.